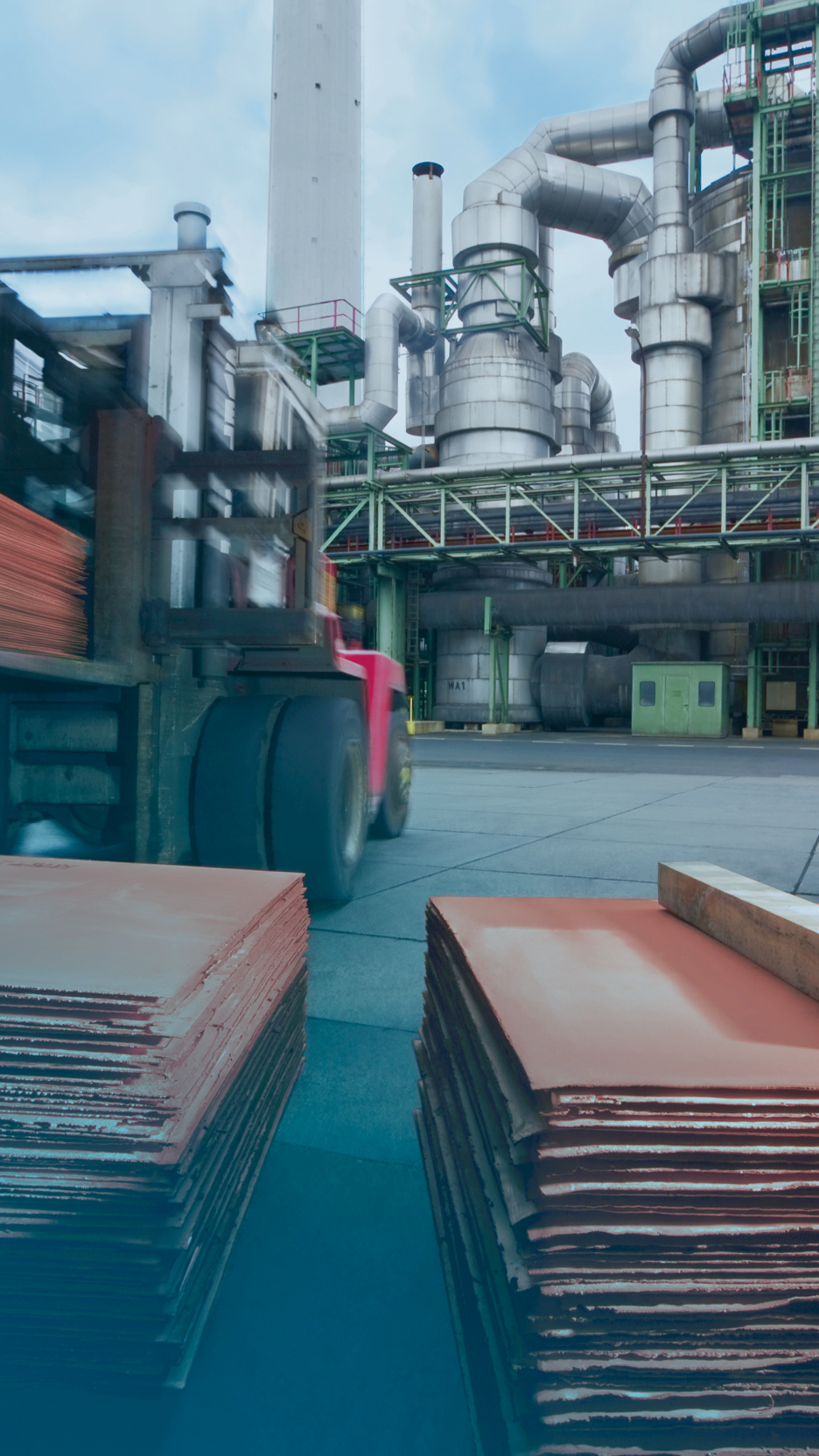
We secure
business
We leverage innovative power, investments and sustainability to increase the strength and scope of our core business. With future-focused processes and state-of-the-art technologies, we are safeguarding our competitive edge and generating lasting value.
Innovative ASPA recycling plant opens in Beerse
We celebrated the opening of the Advanced Sludge Processing by Aurubis (ASPA) plant at our Aurubis site in Beerse, Belgium in early September 2024. “ASPA, a new, state-of-the-art hydrometallurgical process developed completely in-house, is another excellent example of Aurubis’ innovative power. We are pioneers in sustainable metal production and taking recycling to a whole new level,” COO Multimetal Recycling Inge Hofkens said.
Greater efficiency in metal recycling
The ASPA facility processes anode sludge, a valuable intermediate product from electrolytic copper refining at the recycling sites in Beerse and Lünen. The new technique was developed completely in-house using Aurubis expertise and offers two major advantages: quicker recovery of precious metals and the complete recovery of lead and tin from anode sludge. ASPA strengthens recycling in the Group and creates great value for the circular economy.
Construction on the completely new area started in December 2022, and the grand opening took place in September 2024. This around €33 million investment is a clear signal of Aurubis’ commitment to continuing to advance the Beerse site. ASPA links the European sites more closely than ever before. We are generating additional synergies by optimizing preliminary product flows.
ASPA is one of the largest investment projects in Aurubis’ strategic roadmap. It helps us strengthen our position as one of the most efficient and sustainable integrated smelter networks in the world.
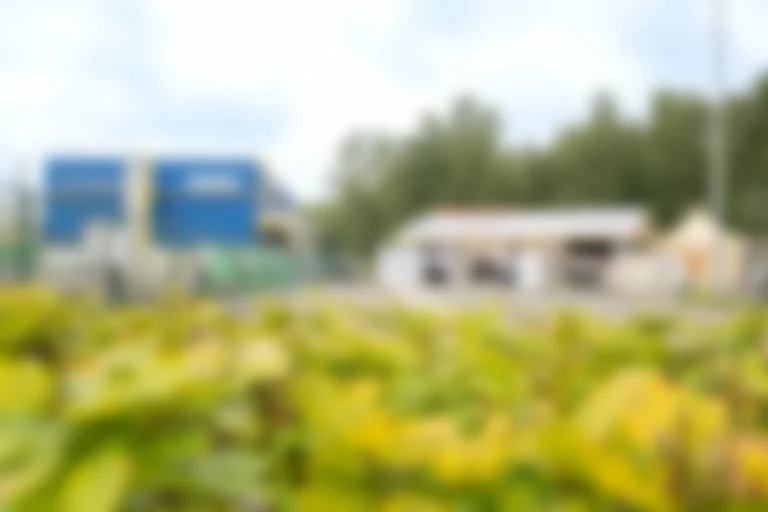
State-of-the-art tankhouse commissioned in Lünen
On June 6, 2024, Aurubis officially commissioned the modernized tankhouse at the Lünen recycling site. €60 million went into this comprehensive refurbishment, which increases production capacity by around 10 % as global demand for raw materials rises. We will now be able to manufacture up to 210,000 t of copper cathodes in Lünen.
Sustainable modernization
Future-proofing the site was an important factor for us. This investment is a commitment to both the site and to protecting the environment. With this long-term approach, we are investing in the plant’s future viability for the coming decades and further securing Lünen’s position as one of the most important Aurubis multimetal recycling sites in Europe. Lünen is a powerful cornerstone of the circular economy and crucial to the success of the energy transition.
In addition to copper, Lünen also processes other metals — such as gold, tin and nickel — into intermediate products as part of operations. Our pioneering approach increases the overall availability of responsibly recycled metals. Modernization started in 2020 and included overhauling the tankhouse basins, renovating the infrastructure, and investing in state-of-the-art robotics. We were able to continue running the plant at about 80 % capacity despite construction.
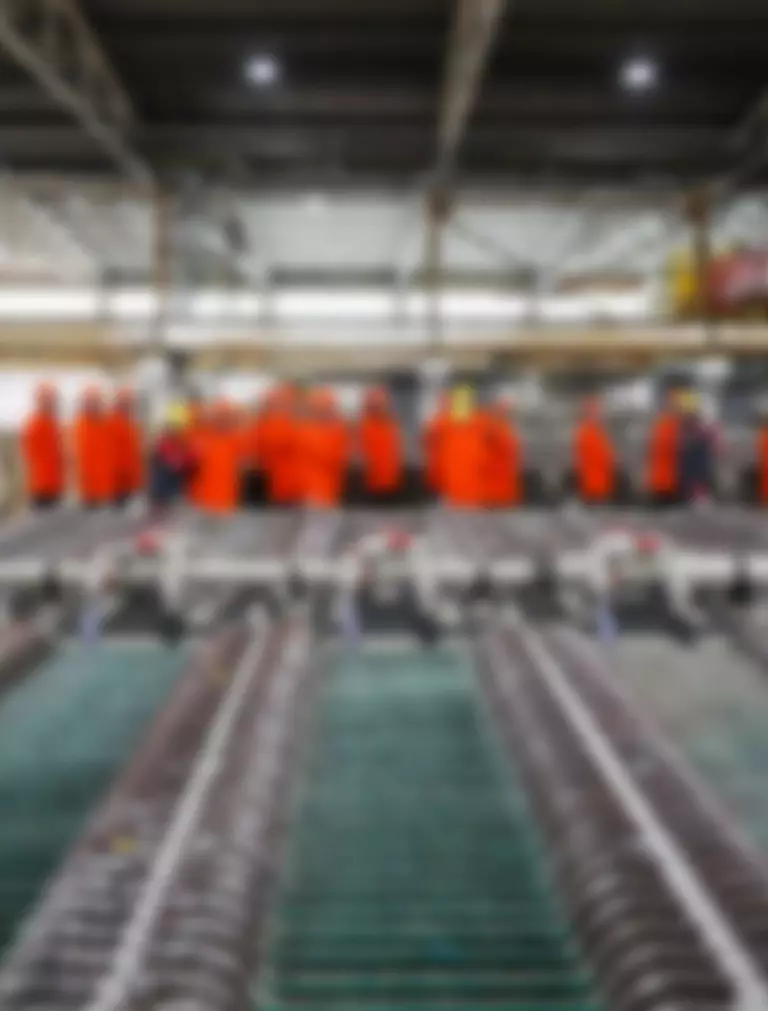
Electrowinning pure copper
Electrolysis is the final step in the copper refining process. Copper anodes — plates weighing about 400 kg with a copper content of up to 98 %, recovered by melting down recycling raw materials in multiple upstream steps — are electrochemically dissolved in the tankhouse. The copper ions are deposited on stainless steel plates, resulting in 99.99 % pure copper for optimal conductivity in downstream applications. The other substances contained in the anode, such as precious metals, precipitate out during electrolysis and are then separated out in additional steps and refined in the Aurubis Group network.
Aurubis Hamburg completes the largest maintenance shutdown in its history
On July 11, 2024, we wrapped up the largest scale maintenance shutdown in the history of the Hamburg site.
This investment is a clear commitment to the Hamburg site. We completed around 500 individual projects during the scheduled maintenance and modernization work and invested roughly €95 million. The scope included important steps like technically inspecting the waste heat boiler, updating the flash smelting furnace, and installing a new heat exchanger in the contact acid plant. These projects considerably boost energy efficiency and enhance environmental protection. We also installed a tap hole drill and tamping machine, which will automate slag tapping in copper production in the future, heightening occupational safety.
We have invested extensively in the digitalization and automation of our production equipment during maintenance shutdowns in recent years. These modernizations allow for even more efficient and stable production processes and ensure challenges are identified at an early stage so countermeasures can be initiated in good time. This optimized basis allows us to extend the maintenance cycle at our primary smelters from two to three years. We are unwaveringly pursuing our goal of further increasing our already high system availability.
Key measures included technically inspecting the waste heat boiler, updating the flash smelting furnace, and installing a new heat exchanger in the contact acid plant.
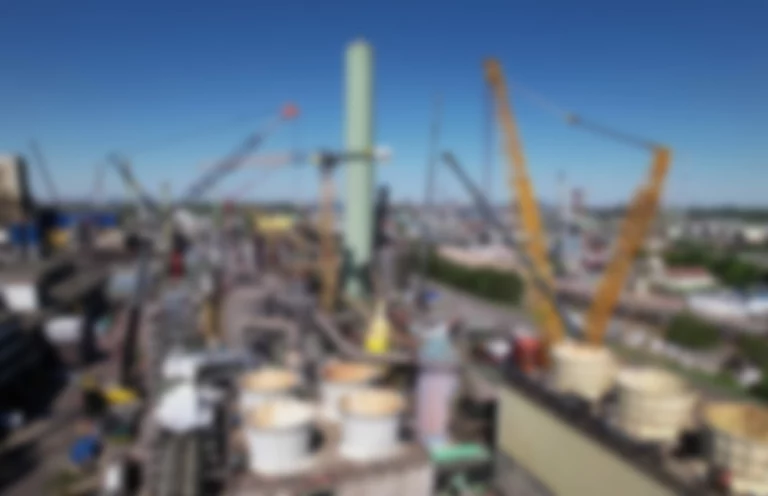
BOB recovers metals from bleed
Aurubis inaugurated the new Bleed treatment Olen Beerse (BOB) plant at the Olen (Belgium) site in December 2024.
BOB uses a hydrometallurgical process to recover valuable metals such as nickel and copper from the electrolyte streams generated during electrolysis in metal production at the Aurubis Beerse and Olen sites (both in Belgium). The facility comprises a complete tankhouse purification system known as bleed treatment.
Optimizing material flows
BOB allows Aurubis to take over another part of the multimetal value chain and optimizes Group-wide material flows by processing electrolyte streams from Beerse and Olen. BOB is an important building block in our strategy. We consistently strive to use raw materials and intermediate products even more responsibly to contribute to a powerful European circular economy.
Pioneer in sustainability
The recycling plant also meets the strictest environmental standards in Belgium and Europe. More proof that Aurubis is a pioneer in sustainable metal production.
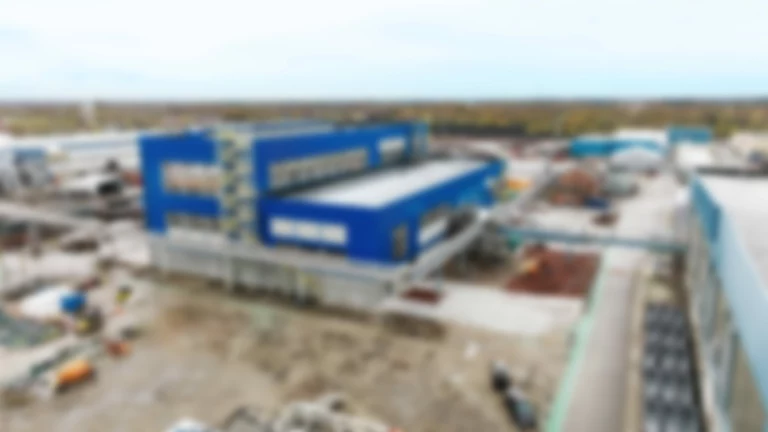
A whole new level of the circular economy
At the heart of the Complex Recycling Hamburg (CRH) project is an innovative plant that will combine the separation and further processing of valuable raw materials and decisively increase our capacities for recovering metals from intermediate products resulting from copper production. CRH gives us the ability to process copper-lead matte, an intermediate that contains copper, lead, sulfur and precious metals, in-house in the future, extract valuable new raw materials like blister copper, sulfur dioxide, and lead oxide, and process them further in our smelter network. The project involves an investment volume of about €190 million and will allow us to treat an additional roughly 30,000 t of recycling material per year along with larger amounts of complex smelter intermediate products. This innovative process enables the highest value recovery rates and reliably closes important material cycles.
Developed especially for this project, the process improves the utilized capacity of our existing equipment and expands the metallurgical capabilities of the Aurubis smelter network. This means we can advance our competitive position and make precious metal processing more efficient through quicker process times.
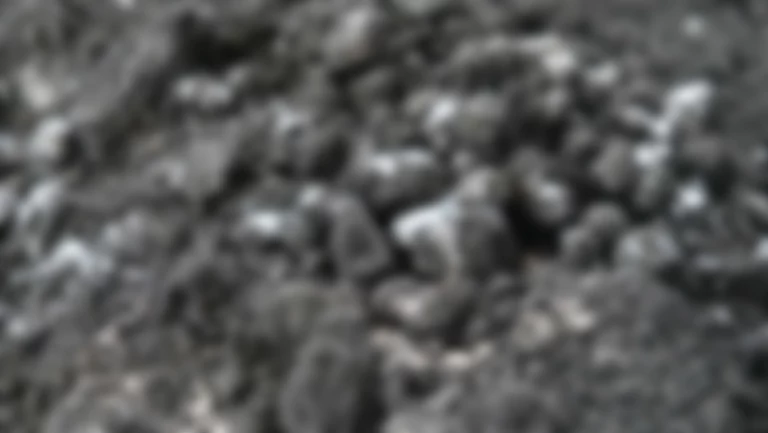
“No other growth project optimizes as many value streams and is so closely integrated into our smelter network as CRH.”
— Jürgen Jestrabek, Complex Recycling Hamburg Project Manager
Watch this video to learn more
Aurubis gives the site and copper production a boost
In April 2024, we started the tankhouse expansion for copper production in Pirdop, Bulgaria. Bulgarian Minister of Economy and Industry Dr. Petko Nikolov was present for the official kick-off of an investment that impressively underscores our strategic focus, Driving Sustainable Growth. With a total investment of around €120 million, the project is a huge step forward for both the Pirdop site and for strengthening our core business in copper refining. Completion is scheduled for the 2025/26 fiscal year.
“The Pirdop site is a cornerstone of the smelter network for Aurubis.”
— Tim Kurth, COO Custom Smelting and Products
Expanding the tankhouse in Pirdop will increase annual production capacity on site by 50 %, to a total of 340,000 t of refined copper. This essential metal for the energy shift and digitalization is in higher demand than ever. The capacity expansion in Pirdop is our contribution to meeting this growing demand and reinforcing European supply security. Our focus is on enhancing not only the volume but also the efficiency of our copper production, and processing all of the anode copper produced in Pirdop directly on site in the future. This also reduces our logistics costs and, consequently, our Scope 3 emissions.
The tankhouse expansion is part of an extensive investment program in Pirdop that aims to make the site fit for the long-term future. For example, we are installing around 460 high-efficiency engines and modernizing transformers and lighting technology, significantly improving energy efficiency. These modifications will prevent around 12,000 t of CO₂ emissions a year and are instrumental in helping us achieve our target of carbon-neutral production well before 2050.
Aurubis has been a key industrial investor in Bulgaria since 2008 and plays a decisive role in the country’s economy. The tankhouse expansion and resulting increase in copper output demonstrate our confidence in the Pirdop site and its further sustainable development.
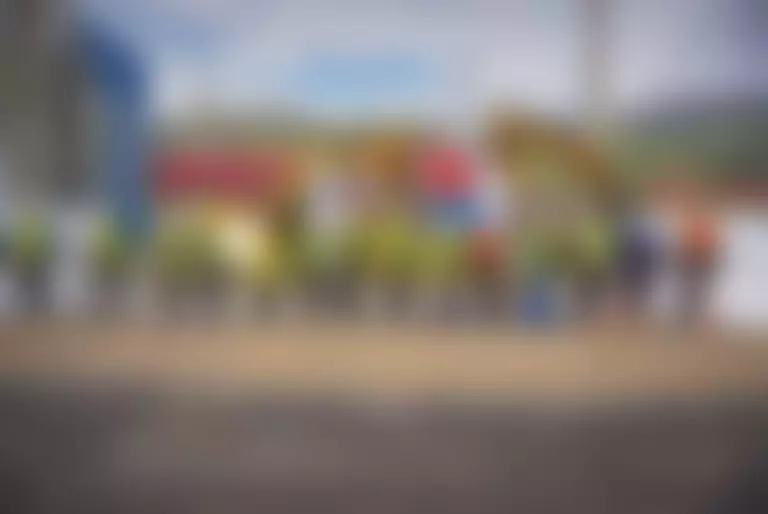
Optimizing slag processing
Aurubis is investing around €46 million in an improved slag treatment process at the Bulgarian site. This project makes an important contribution to protecting the environment. In the future, slags will no longer be cooled in pits but in over 200 slag pots instead. Although the current process is considered good practice in the industry, we are raising the bar for environmental protection with the new method that goes well beyond current standards. It allows us to increase occupational safety on site while also considerably lowering the diffuse emissions produced during slag processing. This investment in an optimized slag treatment process will play a role in getting us to our target of an additional 15 % reduction in specific dust emissions by 2030 compared to the 2018 baseline.
In addition to positively impacting environmental protection and occupational safety, the new process also reduces copper losses in slag and improves metal yield. This allows us to keep an even higher percentage of copper in the production loop. Once scheduled commissioning is complete in 2026/27, we will be able to extract around 500 t of additional cooper a year.
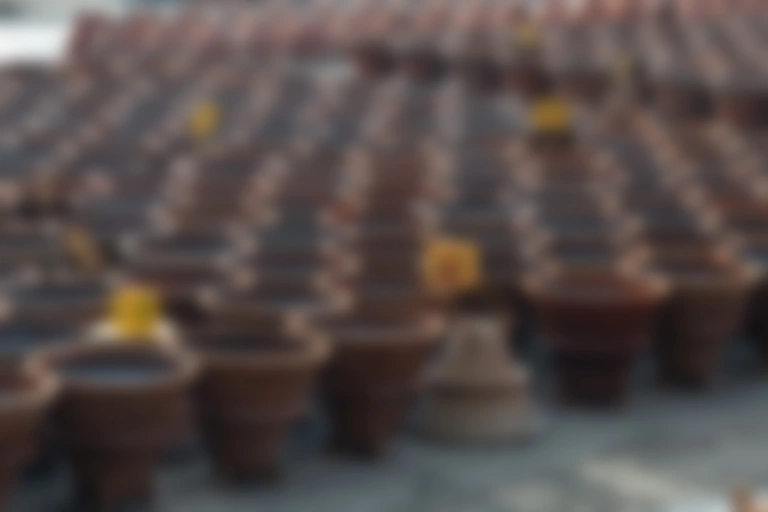
Aurubis is heightening security and setting new standards in process technology and systems engineering
Aurubis is investing around €300 million in a new, innovative precious metals processing plant at the Hamburg site. In combination with the existing equipment, the Precious Metals Refinery (PMR) represents a new, integrated high-security area for precious metal processing at the site. The new refinery is expected to launch in fiscal year 2026/27.
The Precious Metals Refinery in Hamburg brings the entire precious metals processing chain together in one closed security area. The project not only heightens plant and precious metals security and occupational safety; it also sets new standards with innovative process technology and systems engineering. The newly developed metallurgical process will considerably reduce throughput times for materials containing precious metals and lower operating costs by around 15 %. We are significantly raising production capacity for precious metals with this optimization and laying the groundwork for additional strategic growth projects.
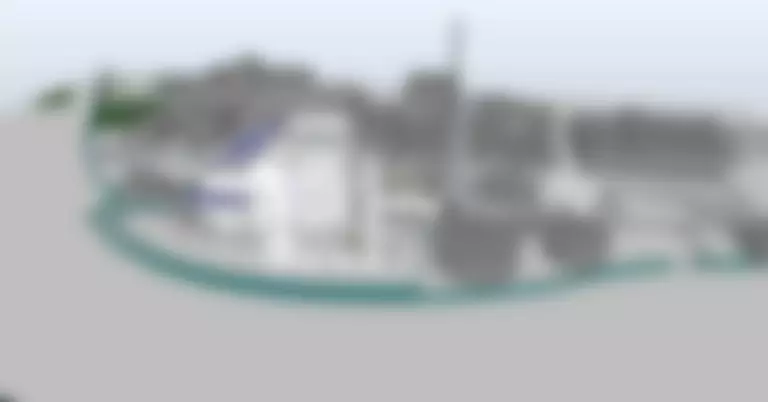