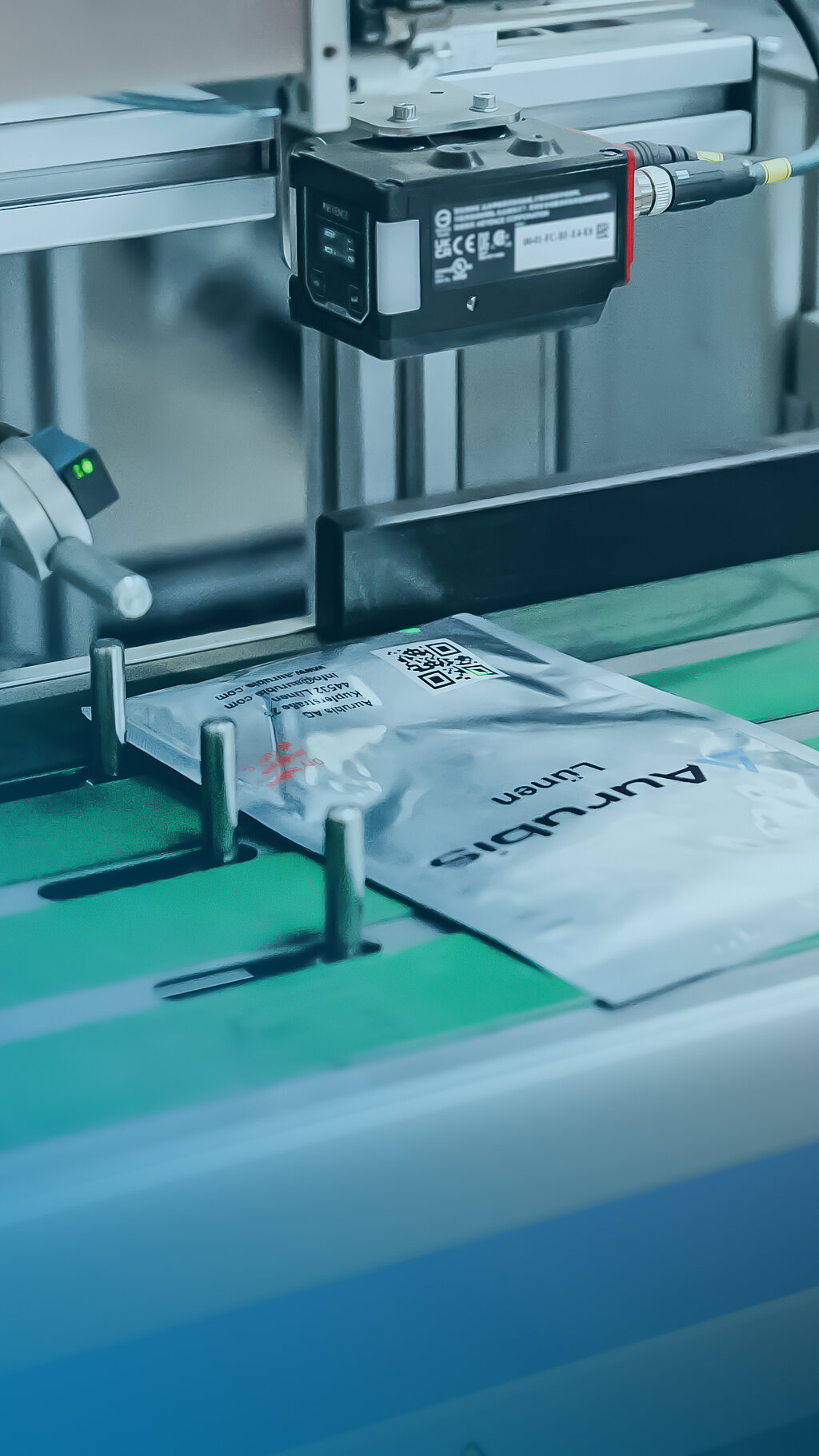
We drive
innovation
With a pioneering spirit and technological excellence, we set new standards in the metals industry. We devise efficient, sustainable solutions for future challenges by actively advancing the automation and digitalization of our processes.
Autonomous sample preparation in Lünen
In February 2024, we launched an innovative system for fully automated e-scrap sample preparation at the Lünen site. The new equipment reduces the steps that need to be done by hand, increases work safety, and boosts efficiency. A flagship project for the entire Aurubis Group.
Efficient and safe
In Lünen, sample preparation of feed materials, such as e-scrap, is now fully automated with the help of cutting-edge robotics. The system now efficiently and securely delivers reliable samples for the laboratory in just an hour — for a sample preparation process that used to be carried out manually in up to twelve stages and could take up to five days. We are setting new standards in the recycling industry while also increasing our efficiency and improving occupational safety for our team.
Complex materials are processed at the Lünen recycling site to recover valuable metals like copper, gold, silver and palladium. Before they can be recycled, the materials have to be sampled to determine their metal content and the value of it, as well as to decide how best to process them. Aurubis specialists in the laboratory analyze material samples to answer all these questions. The samples have to be ground very fine and must have exactly the same composition as the entire shipment. The new equipment ensures both.
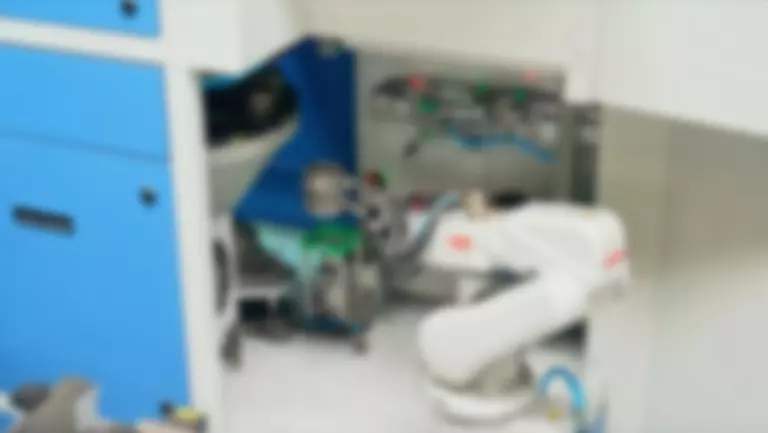
A pilot project for the future of recycling
Processing up to 10,000 samples a year, the system in Lünen is the most powerful of its kind in our sector. It is also the first in the Aurubis Group and a model for other sites. We are investing in a similar system for the Hamburg plant as well, which is scheduled to go online at the start of 2025. The Aurubis plants in Bulgaria, Belgium and the US will follow. And e-waste is just the beginning; thanks to the options the new equipment offers, it will also be possible to efficiently and safely sample copper concentrates and intermediate products such as slags in the future.
Laying the groundwork for the digital transformation
At Aurubis, the Digital Factory plays a key role in optimizing production processes with the help of digital technologies, automation and robotics. Realizing optimization potential quickly and efficiently is one of the innovation program’s great strengths.
In an increasingly digital world, consistently assessing existing processes and using innovative technology to optimize them is no longer a competitive advantage; it is an economic necessity. The Digital Factory is one way we are meeting this challenge at Aurubis. This in-house innovation program makes a significant contribution to creating the safest and most secure, sustainable and efficient multimetal smelter network in line with our company strategy.
Behind the Digital Factory is an agile team that reports directly to the Executive Board and can quickly execute innovations with no bureaucratic hurdles. The Digital Factory identifies various projects in the five large plants, and the members work together with employees on the ground to identify optimization potential that they then develop and address by implementing concrete solutions. The Digital Factory’s quantifiable successes to date speak for themselves.
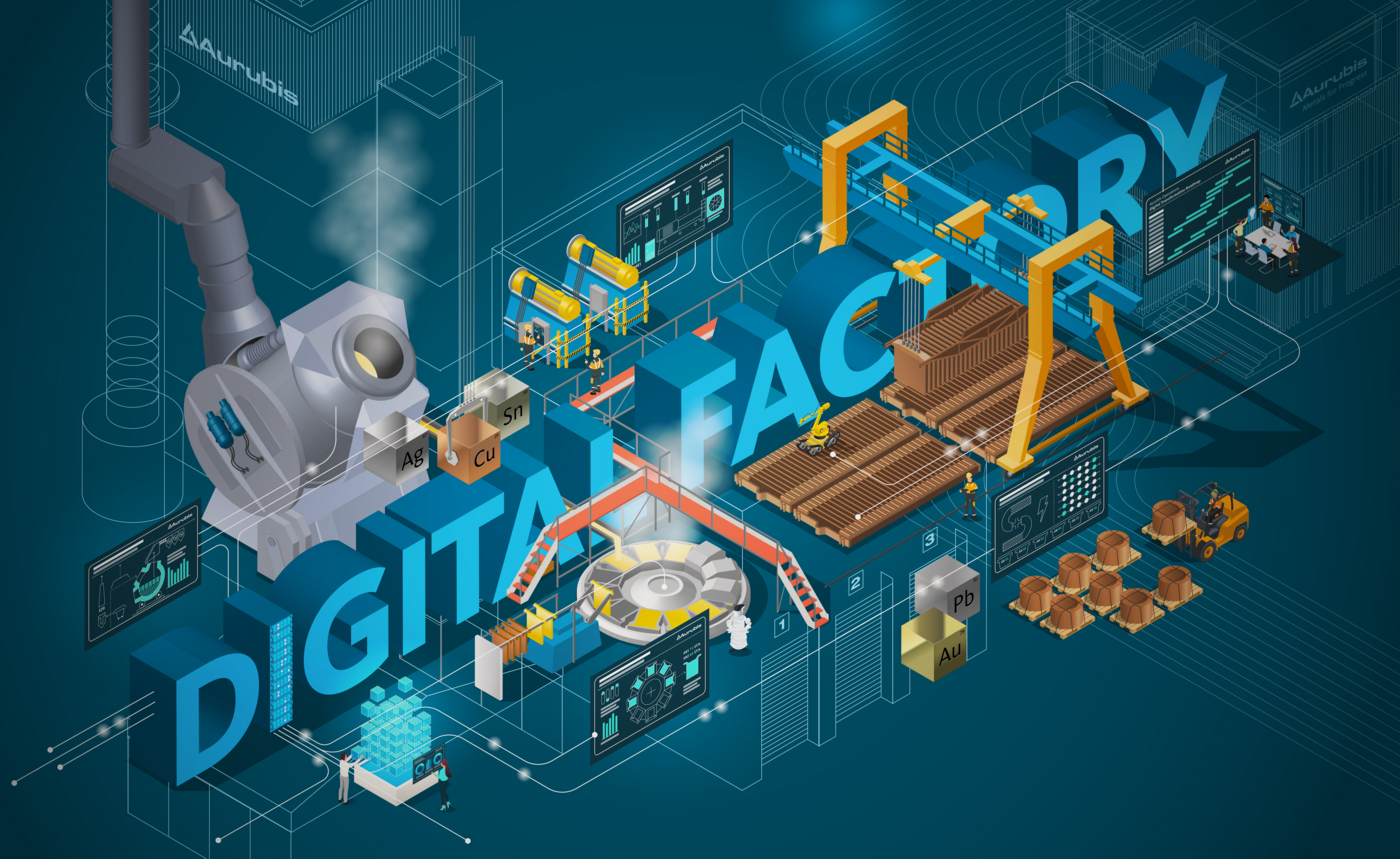
Turning potential into innovation
An energy management project concerning steam generation at the Hamburg site is one recent example of the rapid leveraging of optimization potential. Since August 2024, a system powered by artificial intelligence has ensured that electricity is automatically used to generate steam when prices are low or even negative. The gas-powered boiler takes over steam production as soon as the electricity price is higher than that of gas. Our experts from Energy Management worked as a project team with colleagues from Data Science, Data Engineering, and Operating Technology, and developed this solution for optimized energy utilization in just a few months. The system estimates the plant’s steam and electricity needs every 15 minutes using process data. A link to the electricity market compares prices at the same time. A component supplied by Aurubis subsidiary azeti creates a secure interface between IT and production. This flexibility in energy usage saved €100,000 in the very first month, and could cut costs by an annual €840,000 in this facility alone.
Digitalization along the entire value chain
Digitalization offers Aurubis an enormous opportunity to design production processes more precisely and efficiently than has previously been possible. All production processes from smelting to final processing are monitored and controlled using sensors. So digital solutions like artificial intelligence can be used along the entire value chain to help optimize processes, increase equipment availability, and lower the amount of maintenance needed. This transformation not only boosts production performance; it also reduces energy consumption and minimizes sources of error.
More efficient, sustainable, safe
The Digital Factory is not a rigid structure. A variety of different divisions work together under the umbrella of this program, driving the digital transformation of production processes at Aurubis: the Digital Transformation managers at the plant sites, Data Engineering, Data Science, Modeling and Optimization, IT Production, Group Continuous Improvement, Research & Development, and Operating Technology. Together we develop solutions tailored to meet the specific needs of the facilities and projects in the respective plants. This not only promotes the acceptance of new technologies; it also accelerates their implementation. Condition-based monitoring at the Olen, Belgium site is one example of this development. Sensors and real-time data are used to monitor the smelter furnace cooling blocks in order to detect potential problems early and conduct preventative servicing. This helps prevent unplanned shutdowns and extends the useful life of the equipment.
Securing the future
We leverage the full potential of our integrated smelter network by linking the sites with real-time information and analyses. The focus here is on security, efficiency and sustainability. Automated processes and robotics also improve occupational safety and create a positive working environment that is centered on people and the activities they undertake to add value. The 2030+ target images developed by the Digital Factory show what these steps could look like in reality and which concrete projects are being realized. The target images unite our production processes with the innovation projects in implementation and provide a clear, project-based roadmap for the future. A simplified example of a 2030+ target image can be viewed below.
In the years to come, the Digital Factory program will continue to play a key role in advancing and implementing forward-looking technologies at Aurubis. We are securing our future by means of intensive exchange between production sites and by continually tweaking all processes with technological innovations.
Tankhouse target image
This picture shows what tankhouse processes might look like in the future: safer and more sustainable, with more throughput, less maintenance effort, and increased facility availability.
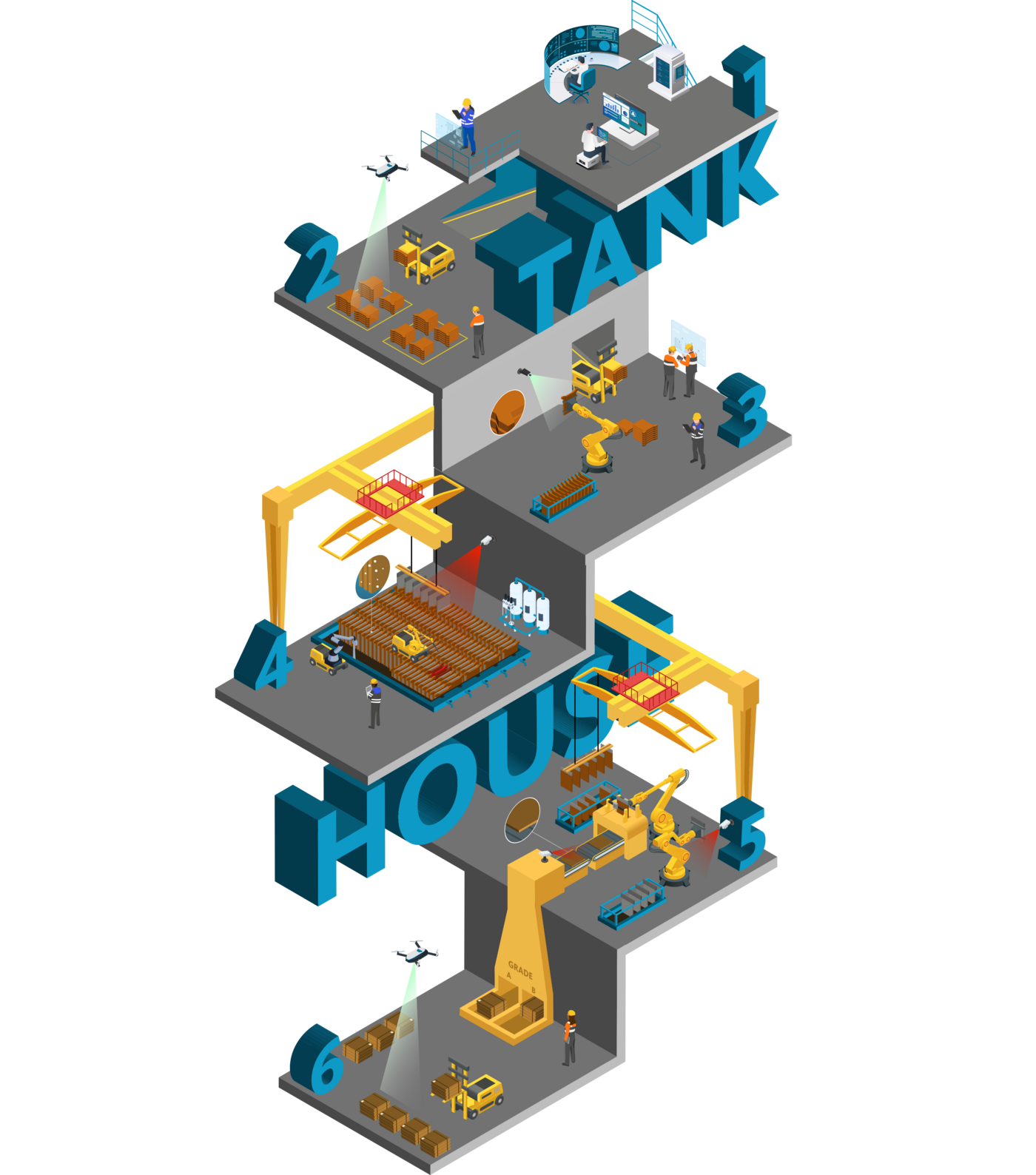
1. Control & maintenance
Sensor and camera data helps transparently and thoroughly track and control production processes.
2. Warehouse
Autonomous transports and automated anode recognition boost throughput and safety.
3. Quality assurance
Predictions made by artificial intelligence (AI) and depth cameras contribute to optimizing processes.
4. Tankhouse
From loading the anodes to removing the cathodes, automated production steps contribute to efficiency and safety.
5. Cathode management
Depth cameras analyze the cathodes to identify necessary maintenance or process improvements.
6. Cathode transport
Automated transport systems mean transparent inventories and more security.