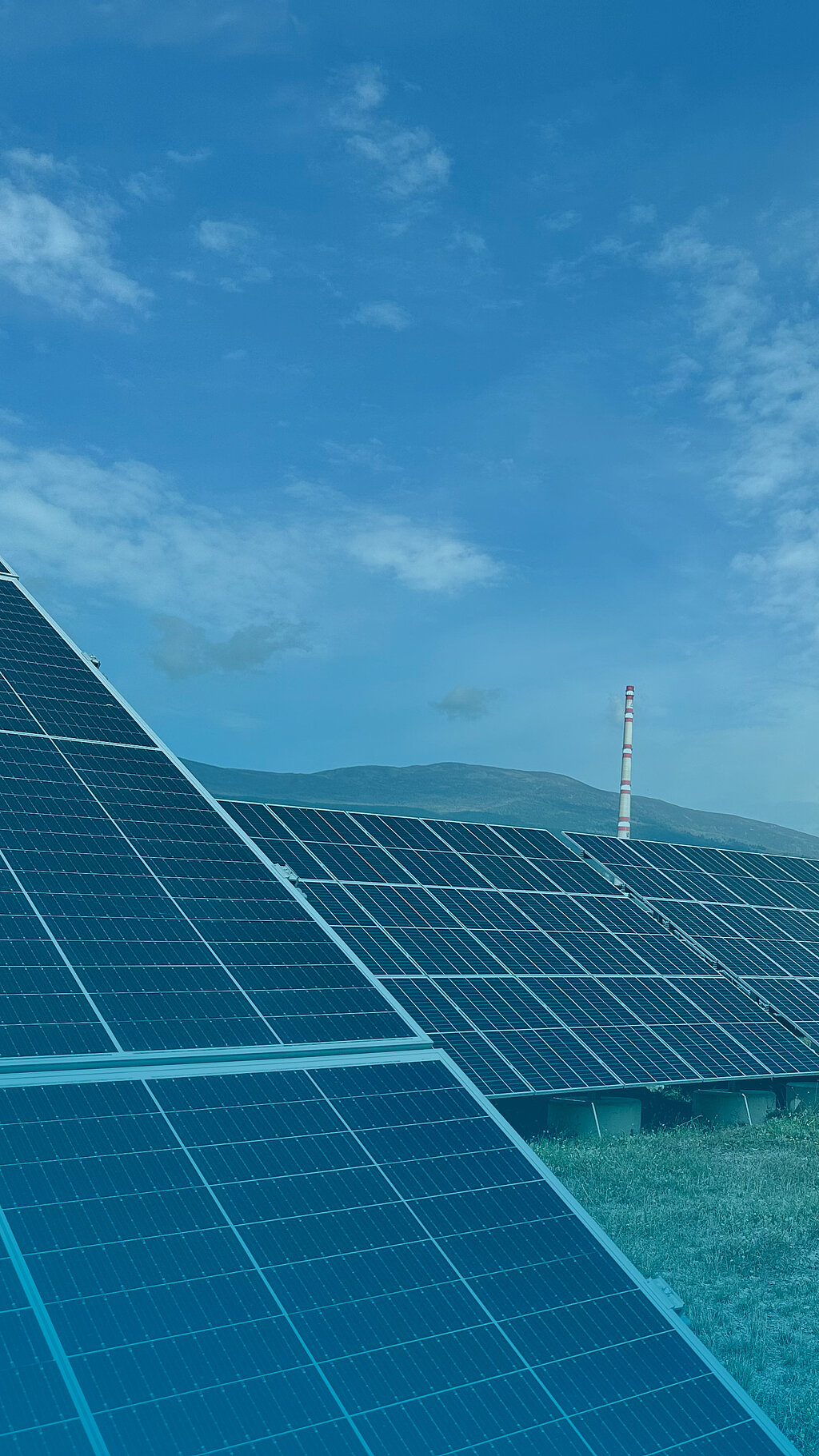
We ensure
sustainability
Sustainability is at the center of our actions. We are continuously working on using resources more efficiently, cutting emissions, and enhancing safety at Aurubis. We set benchmarks in the industry and promote the alignment of ecological, social and economic values. In doing so, we make an active contribution to protecting our planet and securing sustainable value creation for the coming generations.
Sustainability strategy and targets at Aurubis
Aurubis is pursuing an ambitious sustainability strategy, which is a fundamental part of the company strategy, Metals for Progress: Driving Sustainable Growth. Our company strategy is based on three pillars: securing and strengthening the core business, pursuing growth options, and expanding our industrial leadership in sustainability. We are demonstrating that economic success and sustainable activity are inextricably linked.
To achieve our strategic sustainability agenda, we have also significantly expanded our Sustainability department over the past two years. We have directly integrated the central topics of decarbonization and supply chain management in the organizational structure and created two specialized workstreams to address them effectively. The workstreams unite expert teams that work closely with the relevant departments. We ensure the new structure delivers targeted, effective implementation of the sustainability targets by consistently driving measures to reduce CO2 emissions and optimize supply chain processes.
2030 sustainability targets
We have set ambitious targets until 2030 that are both specific and measurable, and allocated them to the action areas of people, environment and economy.
By extensively integrating sustainability in the company strategy, Aurubis demonstrates that economic success and sustainable activity go hand in hand. The demanding targets for 2030 reflect our commitment to advancing sustainable solutions in every area, actively contributing to an innovative world that is ready to face the future.
More information is available here.
Aurubis on the path to carbon neutrality
Aurubis set the target of cutting its direct (fuels) and indirect (electricity) CO2 emissions in half by 2030 — compared to 2018. Furthermore, production should be carbon-neutral at all sites in the smelter network — that is, their processes should be fully decarbonized — well before 2050.
Christian Hein, Head of Decarbonization, and his team concentrate on exactly that: the further development and coordination of the Group-wide decarbonization strategy and the projects to uphold this roadmap and, in the best case, even speed it up.
“On the one hand, we have to think broadly and with an openness to all technologies because there’s not just one technology that we can use to decarbonize all of our different processes to the same extent and at the same time,” says Christian Hein. One part of the solution is the use of hydrogen, for example. However, it’s not available in sufficient quantities or at competitive prices yet. Burner technology is not yet advanced enough either.
That is why Aurubis is currently researching and testing different decarbonization technologies and approaches to develop the best possible solution for everyone.
To facilitate an effective approach and develop best practice measures, the Decarbonization team has initiated three new formats. For instance, there is now an annual Group-wide decarbonization workshop for the sites and relevant Group functions. In addition, once per quarter working teams meet to discuss their experience with concrete projects and technologies — and on a specialist level, the Decarbonization team communicates with the sites about the current progress in achieving the targets, their individual challenges, and possible solutions.
Hydrogen-ready anode furnaces
Green hydrogen is considered a key technology for reducing industrial CO2 emissions. For our anode furnaces too, we see great potential for this techology. We have installed two hydrogen-ready furnaces based on the promising results of a test series carried out in 2021. With an investment of €40 million, we will prevent up to 5,000 t of CO2 per year in the future. This helps further reduce the carbon footprint of Aurubis copper, which is already low within the industry. Our new furnaces also provide additional flexibility for processing even more complex metal-bearing concentrates more efficiently.
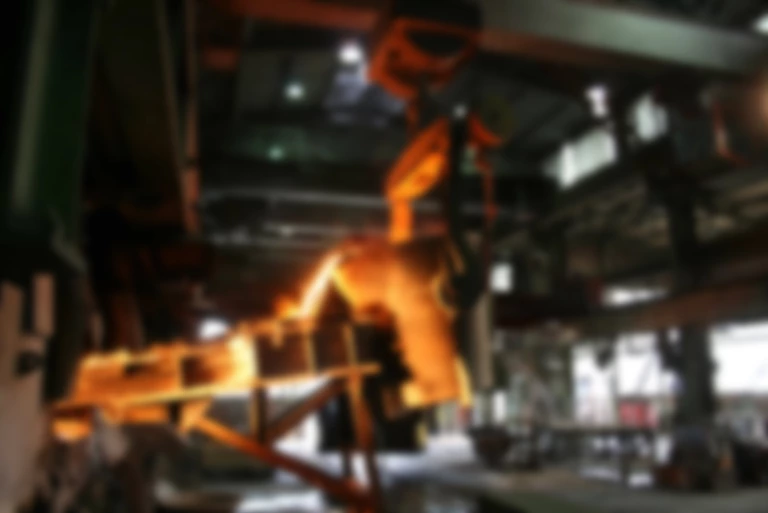
Watch the video about our hydrogen-ready furnaces
Industrial Heat expansion
Since 2018 Aurubis has been using industrial waste heat from the production process at the Hamburg site to supply the HafenCity East neighborhood with CO2-free heating energy. As part of an additional project phase, Aurubis is cooperating with Hamburger Energiewerke, the city’s energy utility, to convert a subprocess of copper production with an investment of about €100 million. Starting in the 2024/25 heating period, this will supply up to 28,000 households with heat, which will cut a total of up to 120,000 t of CO2 emissions each year in Hamburg. The Industrial Heat project, which received funding from the German Ministry for Economic Affairs and Climate Action (BMWK), is the largest of its kind in Germany.
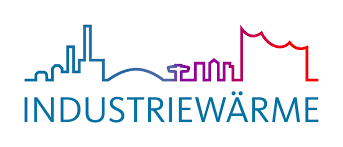
.
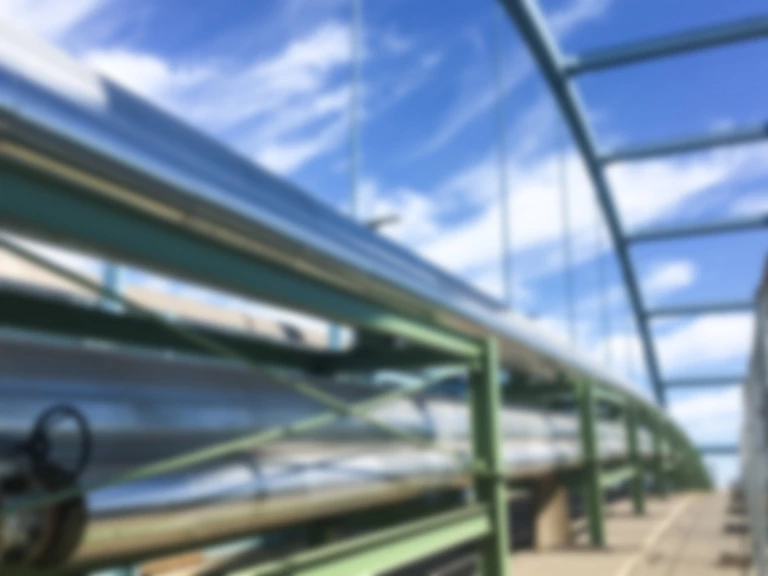
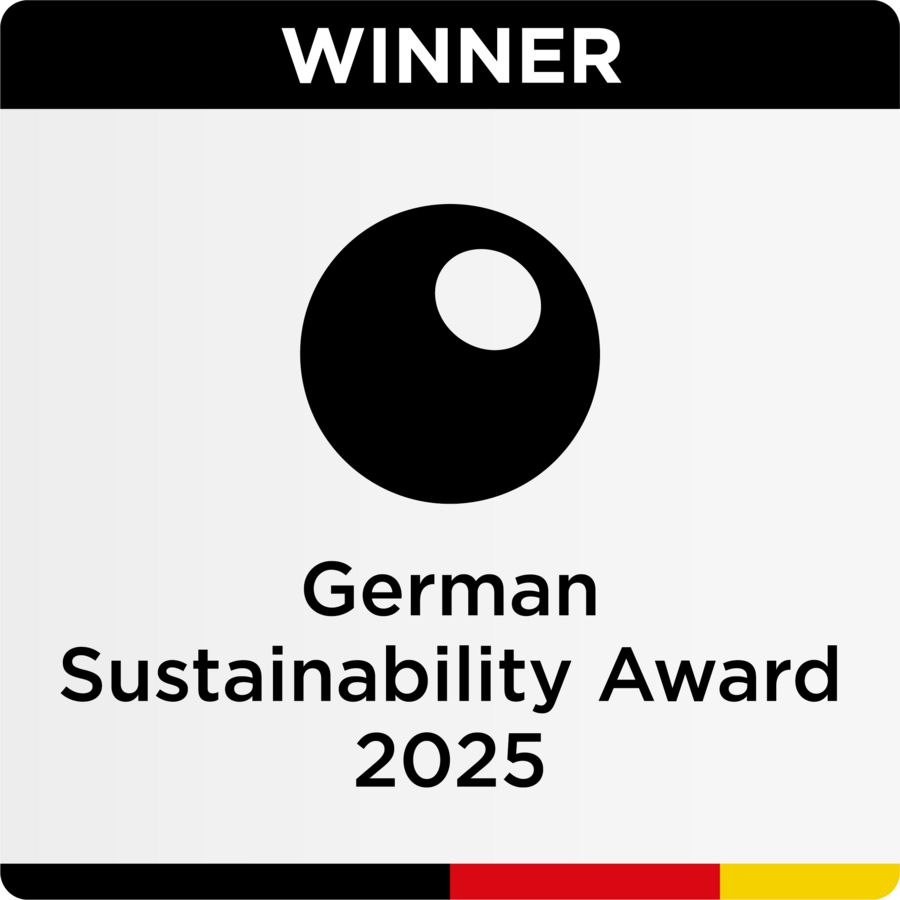
Aurubis received the 17th German Sustainability Award for the metals industry in November 2024. The Europe-wide prize honors our commitment to carbon-neutral production and the circular economy. The distinction confirms our intensive dedication to handling natural resources responsibly. We are pursuing ambitious sustainability targets by means of a number of measures at the international sites for conscientious production that protects the climate and environment. Our commitment to responsible metal recovery contributes to our goal of being the most sustainable and efficient smelter network in the world. Aurubis pursues sustainable business activity driven by its company strategy; this is expressed in Tomorrow Metals, a promise to our customers.
Expanding the Aurubis solar park in Pirdop — another stride towards decarbonization
As part of our long-term Metals for Progress: Driving Sustainable Growth company strategy, we began construction on two additional photovoltaic parks at our site in Pirdop, Bulgaria in April 2024. An additional expansion has already been approved. We have been expanding the captive solar park at the site since 2021, another investment in decarbonizing our production. The expansion will take place in multiple stages until 2024/25.
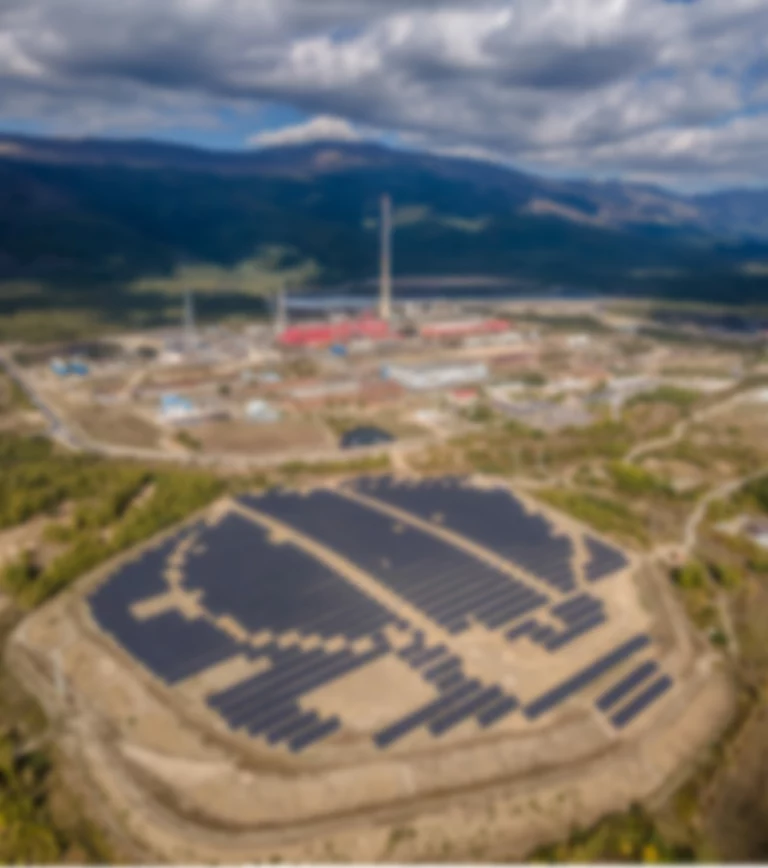
The energy generated in Pirdop flows directly into production processes at the site, allowing us to further reduce the amount of energy drawn from external sources and improve our production’s energy efficiency. Expanding the solar park in Pirdop highlights our ongoing dedication to protecting the climate and promoting resource-efficient production, contributing to our target of becoming climate neutral well before 2050.
We are considerably increasing captive power generation with the four photovoltaic plants that will cover around 15 % of the site’s electricity needs with green energy in the future. Around 55,000 MWh of electricity will be generated every year, roughly the amount required to power a city of 25,000 people. And we will be avoiding around 25,000 t of CO2 emissions per year. This investment in Pirdop increases Aurubis’ independence from price fluctuations on the energy market and is an important step towards carbon-neutral production.
By expanding the solar park we are not just contributing to reaching our own climate targets; we are also helping meet the global climate targets set out in the Paris Agreement. Along with ecological benefits, expanding the solar park also helps stabilize energy costs, thus strengthening our competitiveness on international markets. As energy prices rise, this investment in renewable energy will be a decisive factor in securing our business model over the long term.
The strategic project is part of a comprehensive investment program that will make the Pirdop site more efficient and prepare it for the future. Enlarging the solar park also spotlights our role as a pioneer in sustainable industrial production. We will continue to promote innovative solutions to drive the circular economy and minimize our ecological footprint — for a sustainable future that conserves resources and protects the planet.
Making Aurubis safer
After the serious incidents related to occupational safety and plant security last year, further expanding and improving the safety and security culture is one of the new Executive Board team’s top priorities — and both are now the direct responsibility of COO Custom Smelting & Products Tim Kurth.
At Aurubis, we approach safety and security with a fresh perspective every day and actively put them into practice — hand in hand with productivity and quality. We want to be the benchmark for occupational safety and site security in our industry; this is a goal that everyone in the company contributes to. We are working on Project SAFE for plant security and the TOGETHER occupational safety program to enhance our safetyand security culture and to integrate preventative measures in order to achieve the goal of a safe, secure company without accidents or crime.
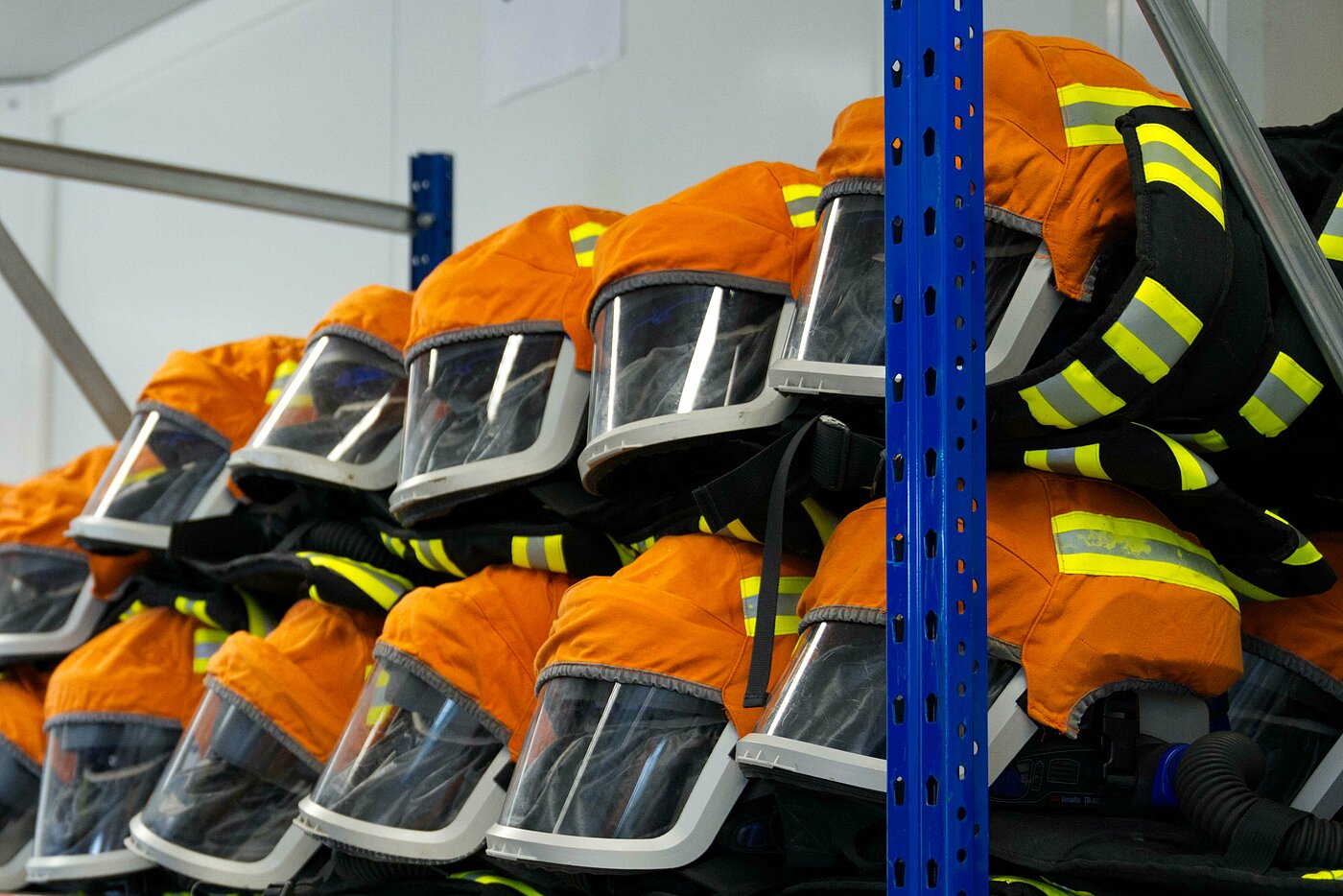
Working safely
Safe work is the foundation of our company’s business success. We are pursuing a clear vision: zero work-related accidents. Our TOGETHER program provides important leverage. With a multistage analysis involving the employees and gap assessments at all sites, we worked with the support of external experts to identify our potential for improvements in occupational and process safety.
We are boosting our leadership culture and empowering our management when it comes to safety risks. We will better identify risk scenarios and the effectiveness of our existing safeguards while establishing suitable additional measures for improved process security.
In collaboration with the Group Health & Safety department, the plants are developing individual action plans to protect employees and the entire company as much as possible. This includes training, regularly exchanging information, and a wide range of technical precautions: from markings, signposting and control and warning systems to state-of-the-art personal protective equipment (PPE) that meets the respective requirements of the plants.
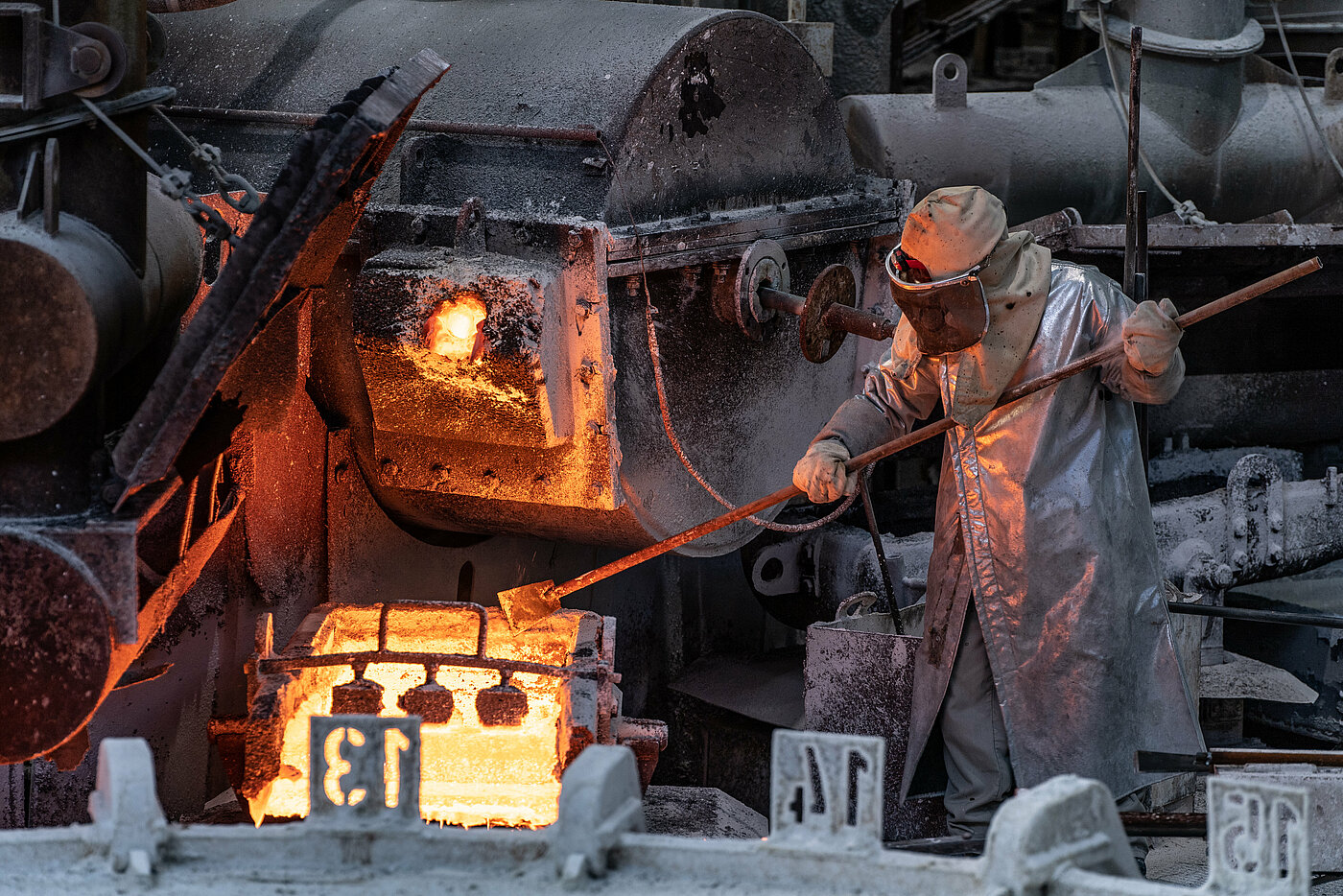
Initial successes with the TOGETHER program
We are actively shaping a safe and sustainable occupational safety culture with the TOGETHER program. We offer coaching for management staff at the Hamburg plant, for example, to increase the effectiveness of in-house safety routines, and are applying new methods for minimizing risks and qualification control. This is leading to positive changes: Awareness of existing hazards has grown considerably and open communication with managers is promoting the development of internal networks and the exchange of information about risks and possible solutions. All 1,800 production workers also completed comprehensive risk factor training at the Hamburg plant to ensure that unsafe situations can be recognized and prevented at an early stage.
“Productivity, quality and safety go hand in hand. We want to be the benchmark for occupational safety and site security in our industry, and to be a company free of accidents and crime.”
— Tim Kurth, COO
Safeguarding against crime
Organized crime is increasing: In 2024 alone, fraud and theft led to damage of over €55 billion1 in Germany — a new record, unfortunately. Criminal activity is a growing threat for companies worldwide.
This illustrates that plant security is about more than just protecting our plant boundaries and entrances. It involves protection against terrorism, crime, theft and fraud, but also sabotage and industrial espionage. We process valuable materials at Aurubis, and our products and intermediates are raw materials in high demand from a geopolitical perspective. Our threat intelligence monitors potential risks, both external and internal, including those related to digital, transport and travel security.
Our Project SAFE measures are continuously strengthening the level of security — and even leading the way in some disciplines, such as our new employee protection program. Our internal Group-wide communication campaign to prevent corruption, theft, fraud and information leaks — “It’s up to you. Make the right choice.” — started in mid-November 2024, with the objective of promoting an improved security culture and compliance with legal regulations, raising awareness of possible risks among employees, and providing them with assistance.
In 2024 we created more than 50 jobs and in some cases new functions at site and Group level, as well as bringing in additional IT support to allow us to meet the growing demands of process and plant security and to anchor and monitor the implemented measures in the long term.
Examples of our safety measures
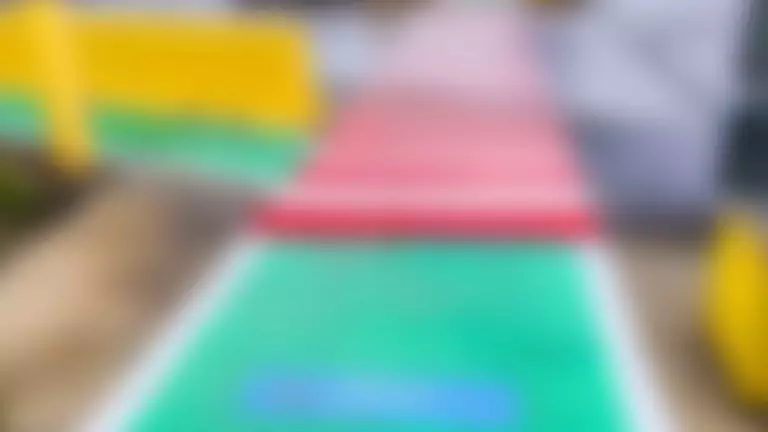
5 questions for Laura Zielinski – Head of Group Human Resources
“Our dedicated, highly qualified experts are committed to deliver.”
The passion and expertise of all employees drive our performance. Laura Zielinski has overseen Group Human Resources since July 1, 2024. In an interview, the manager talks about the challenges and opportunities of successful HR work and about promoting talents.
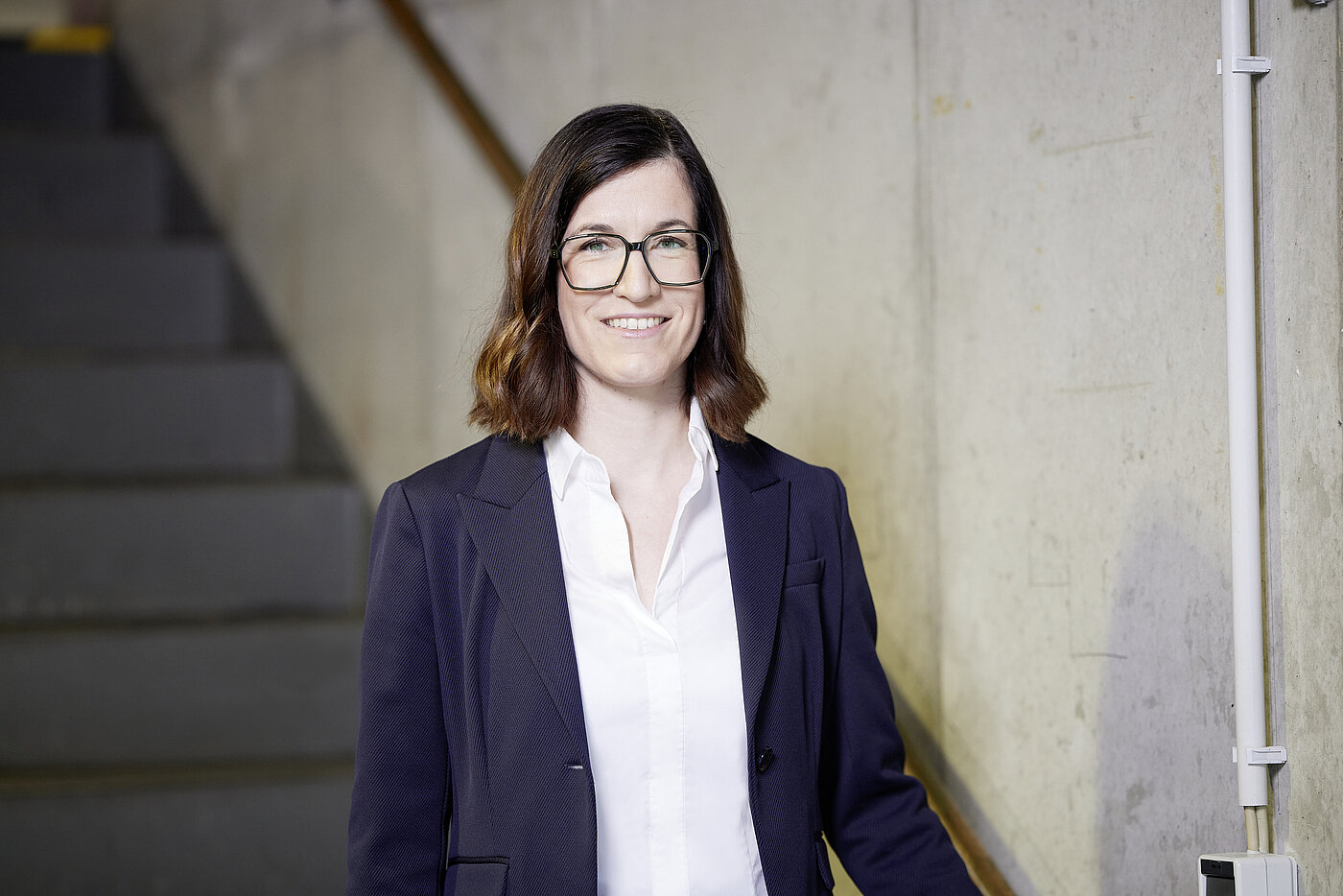
Laura, you started managing Human Resources on an interim basis in October 2023, and now you have been head of the Group department since July 2024. How did the events of last year impact your work?
Laura Zielinski Looking back, I’m proud of how we as a team have overcome the challenges and since been able to regain lost trust with energy and a spirit of optimism — despite difficult setbacks and a lot of upheaval. Our dedicated, highly qualified experts fully stand behind the Aurubis strategy and are committed to deliver. Aurubis Richmond is just one example of how a shared vision, individual performance, and a strong feeling of belonging and appreciative leadership bring about success. We are continuing to deliver on our strategy with the new Executive Board team — and that extends to a forward-looking work culture.
What does a forward-looking work culture in the organization entail?
As a high-performing and reliable company with a clear purpose, we will continue to be guided by this stability in the future. It provides security and forms the foundation for our success at the same time. At Aurubis we are focusing on occupational safety, plant security, and leadership — while continuing to develop our company culture, which is based on shared values, individual commitment, and a clear sense of being part of something. This culture development process requires time and the participation of the entire company. We can only remain successful together.
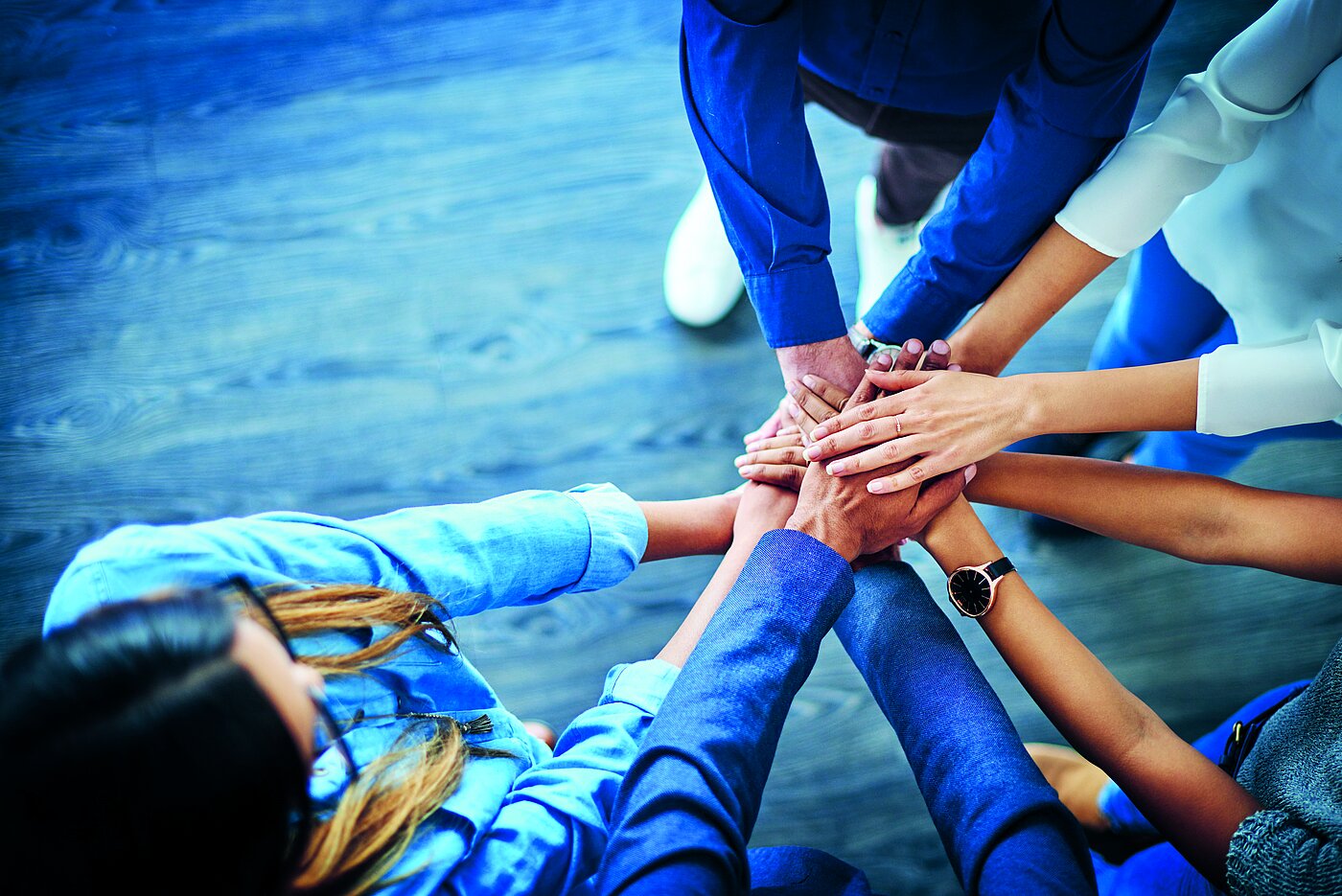
What projects and tools do you use to develop and support employees?
There is a strong focus on performance management and talent promotion in order to activate both individual and collective performance and success. In HR we view ourselves as trailblazers and role models across all sites.
We rely on a number of measures. One central component is our Learning Academy, which provides extensive subject-specific and personal development offerings for employees. We also promote communication and learning with internal learning units. Our international O-Track talent promotion program enables participants to develop their leadership skills, specialized expertise, and project management knowledge. This is how we support ongoing personal and professional development and strengthen our talent pipeline.
How is Aurubis’ HR work perceived — including from the outside?
Our HR work is shaped by innovation, commitment and responsibility, and both internal and external feedback are positive. This demonstrates how high our standards are when it comes to international HR work.
This includes the kick-off of SAP SuccessFactors — which will help us depict the entire employee life cycle from hiring to retirement in the future — and the recognition of our policy on international assignments by the KPMG business consulting firm. I’m especially pleased about the reception of our Women4Metals initiative, which received the HR Excellence Award in 2023. The prize underlines our pioneering role in drawing more women to the industry. Additionally, our diverse mentoring program supports multigenerational dialogue and cross-site development of our talents.
We are sending important signals with respect to diversity, too: By signing the Diversity Charter and initiating sensitivity training relating to diversity issues in recruiting, we advocate for an inclusive company culture and raise awareness of age diversity. We have also introduced a new anti-discrimination policy and appointed a contact person in order to ensure a safe and respectful environment for everyone.
What are some of the future targets and how will you achieve them?
One central target of our HR work is to further enhance trust in management, Aurubis as an employer, and our future as a company, and at the same time to foster a sense of fun about achieving strong performance and developing the Group as a whole. In light of the intense competition for future talents, it is crucial to attract and retain highly qualified employees in the long term. This year we executed a successful campaign to reinforce our employer brand (see below). It centers on people: In an industrial company that produces metals, our employees are the additional key element for our success. We want this initiative to attract talent and create an environment where they can develop and stay with us long-term.
Impressions from the HR Management Conference are available here.
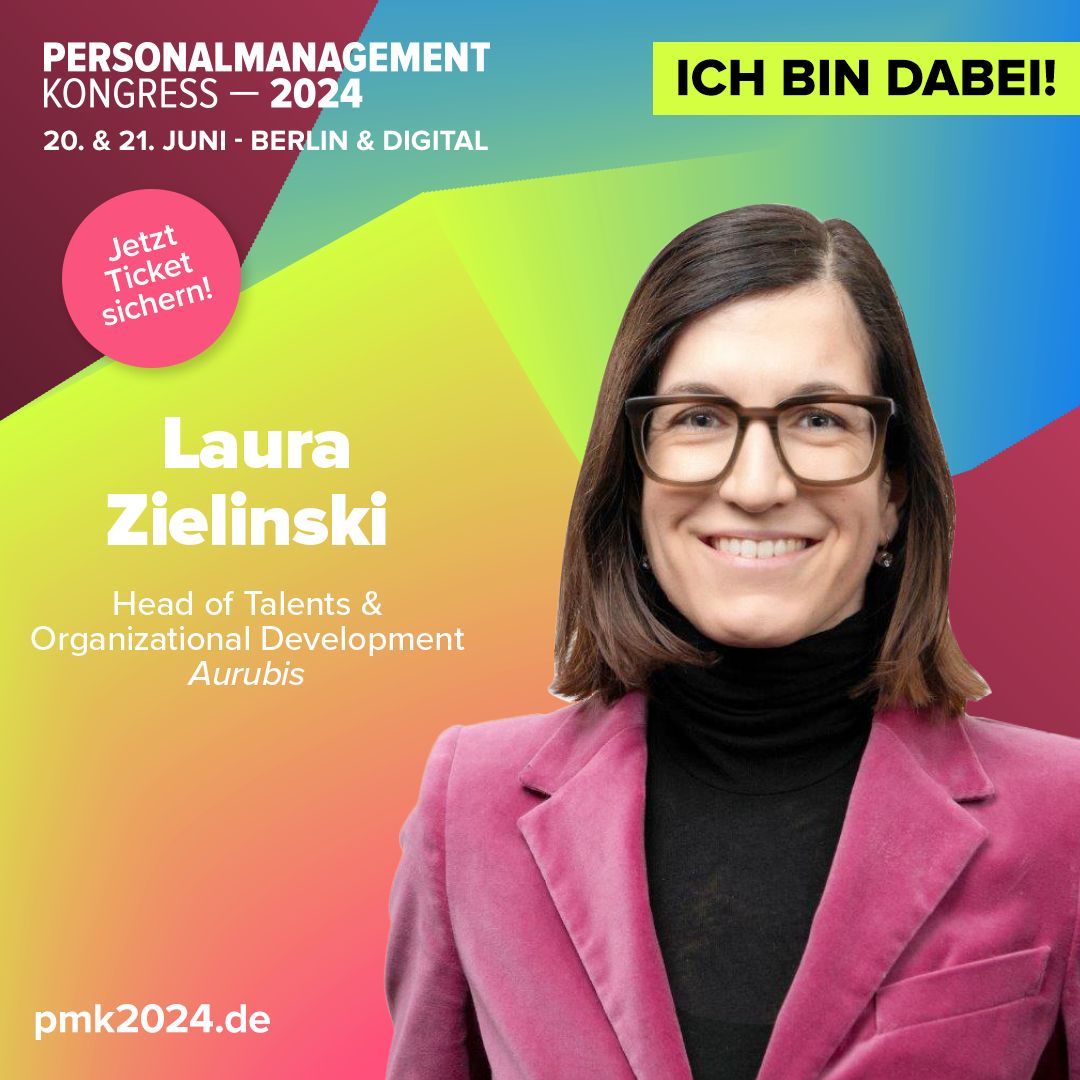
.
Aurubis employer brand: “You are our most valuable element”
Since the end of March 2024, Aurubis has been using this message to present itself as an appealing employer, with a focus on colleagues and their enthusiasm for Aurubis. Based on the periodic table and its 118 elements, the campaign currently includes 36 images from six sites, depicting employees as an additional 119th element — and placing them front and center. Three core elements summarize what makes Aurubis what it is:
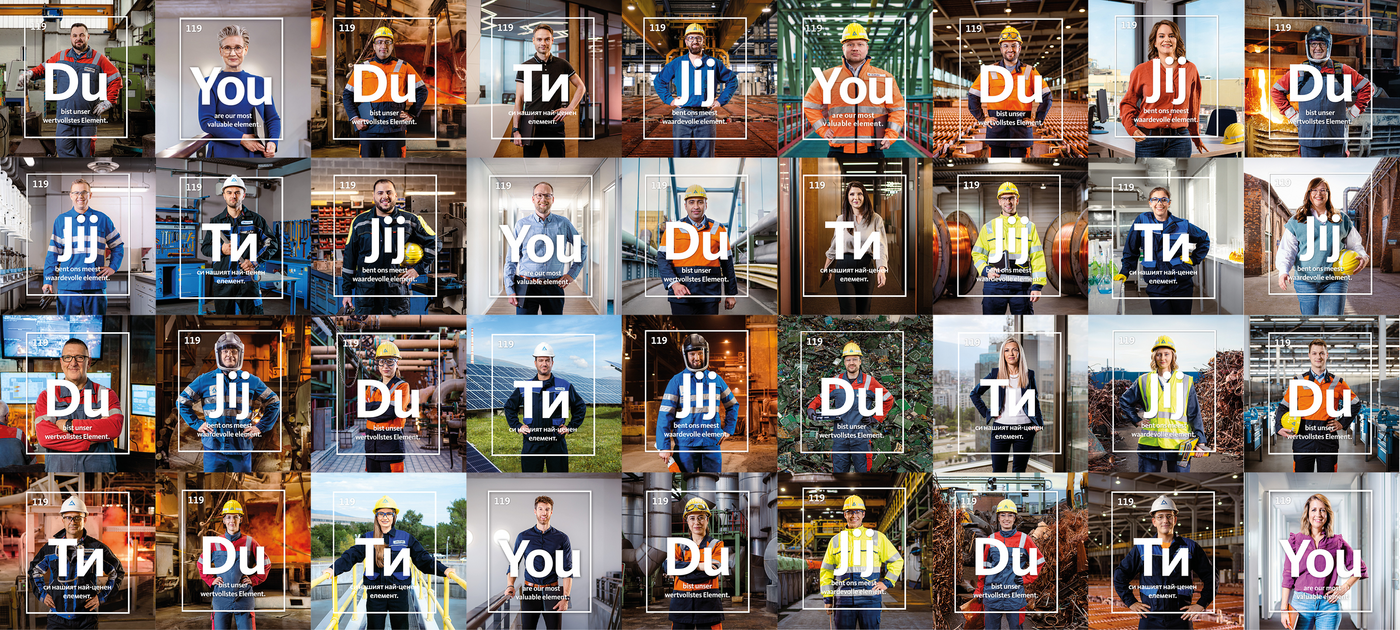
Rock-solid & rolling:
We stand for stability as an employer with our solid business model, even in times of crisis, while developing every day at the same time.
Hands-on & high-tech:
We get down to business — with our passion for metallurgy. We are also advancing our technologies and processes all the time, setting new standards in our industry.
Skilled & seriously sustainable:
We sustainably transform raw materials of various qualities into valuable metals and products daily.
More information on the campaign is available here.
Comprehensive Copper Mark certification of the Aurubis smelter network
Aurubis is expanding its pioneering role in responsible and sustainable metal production by having its smelter network extensively certified by The Copper Mark.1 The Copper Mark is the leading internationally recognized assurance framework for a sustainable and responsible supply chain in copper production.
Following previous certification of the the Pirdop (Bulgaria), Hamburg and Lünen (Germany), and Olen (Belgium) sites, the production sites in Beerse (Belgium) and the rolling mill in Stolberg (Germany) were successfully certified in 2024. Furthermore, the Bulgarian site in Pirdop successfully passed its routine recertification.
With these six sites, this means that all of the large smelters, and nearly the entire Aurubis global smelter network, are fully certified with the Copper Mark. This covers more than 95 % of cathode output that we produce annually by sustainably processing concentrates and recycling materials. It also impressively documents Aurubis’ Tomorrow Metals sustainability promise.
“Aurubis was one of the first supporters of the international Copper Mark assurance framework. This is an expectation we place on ourselves since we advocate for a sustainable copper value chain. We are pleased that all of the large smelter sites, and by volume nearly the entire Aurubis Group, have now been certified in accordance with these exacting sustainability criteria — a milestone for our company,” Dr. Toralf Haag explained.
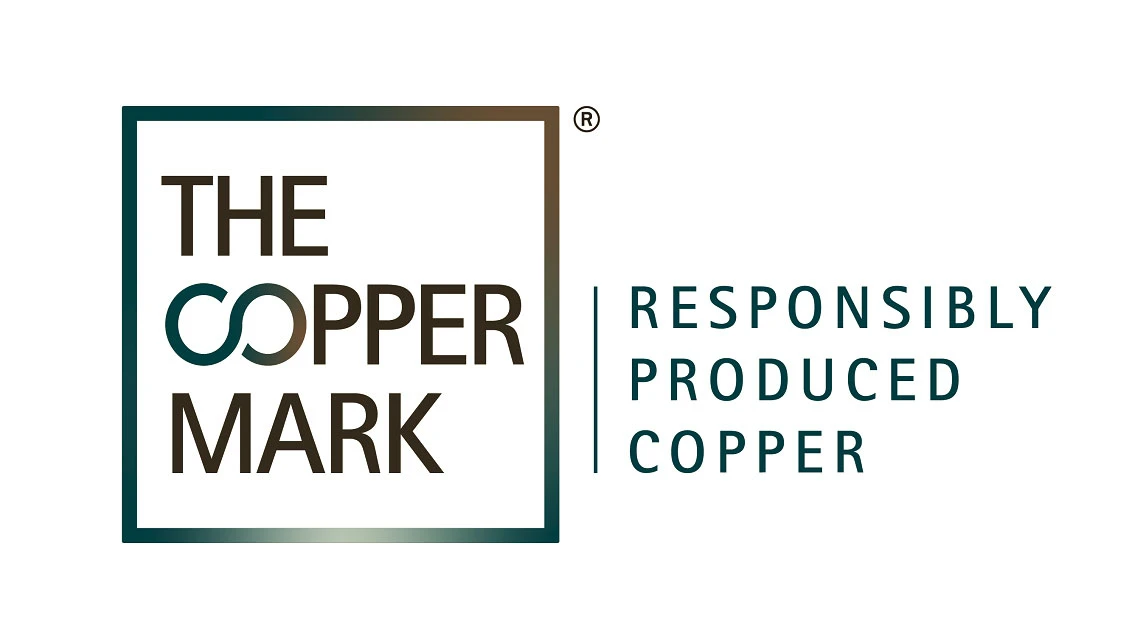
.
Aurubis sites certified by The Copper Mark
1 The Copper Mark is the leading assurance framework for copper, molybdenum, nickel and zinc, with the vision of a sustainable society enabled by the responsible sourcing, production and recycling of these metals. The Copper Mark is working to develop responsible value chains from mine level to the end product. Through the standards and assurance framework, The Copper Mark supports participants in identifying and making on-the-ground changes to their operations. The Copper Mark standards draw on the 33 internationally recognized sustainability criteria of the Risk Readiness Assessment of the Responsible Minerals Initiative (RMI), covering major environmental, social and governance issues. Over 100 copper industry sites have joined The Copper Mark since March 30, 2020. As of today, about 38 % of copper worldwide is produced by Copper Mark-certified sites.
More information about The Copper Mark is available here.
More metals from responsible production
With the goal of continuously improving the production of copper and other elements in alignment with the needs of the environment and people, in February 2024 Aurubis and Chilean mining group Codelco signed an extensive cooperation agreement focused on environmental protection, health and innovation.
Aurubis values long-term business partnerships with companies in the mining industry, such as Codelco. This strategy is crucial for fulfilling the growing global demand for responsibly produced metals. And even though multimetal recycling is playing an increasingly central role, primary raw materials will also be needed in the future to satisfy the growing need for metals for the green transformation. This strategy is how both companies are strengthening the European and global economy, making it more independent and robust in the face of supply chain disruptions.
Our products’ environmental profiles — small quantities, large impact
Copper, tin, silver and gold are key elements that make megatrends such as digitalization possible in the first place. It is therefore crucial for sustainable development that we find environmentally sound ways to produce these important metals.
Our life cycle assessments (LCAs) demonstrate once again that we are leading the way in the industry when it comes to sustainability: Aurubis already produces a number of metals with less than half the average CO2 emissions of its global competitors. The results underline what the Tomorrow Metals label stands for: The carbon footprint of the main product, copper cathodes, has decreased by more than 40 % since 2013. Furthermore, the footprint of the Aurubis plants is more than 60 % lower than the global industry average. Aurubis is more than 55 % below the global average for tin production, and causes over 50 % fewer emissions in gold and silver production. These outcomes reflect the impact of our commitment to sustainable metal production. Our recycling and the effectiveness of our metal recovery play an important role in the results of our life cycle assessments. Recycled material accounted for 43 % of the content of our copper cathodes in 2023, 56 % for silver, and 23 % for gold. For tin, the proportion of recycled material was even 100 %.
More information about Tomorrow Metals is available here.
